January 18, 2021 – Seattle – Swiftsure Group affiliate rfidCollect’s personnel tracking system tracked hundreds of workers, contractors, vendors and visitors at a classified Johns Hopkins Applied Physics Laboratory (APL) site during more than a year of construction.
Skanska, one of the largest construction and development companies in the US, selected rfidCollect to provide the automatic personnel tracking system throughout construction of a building addition at APL in Laurel, MD.
The tracking system, EdgeCollector, delivers a cloud-based, on-premises solution with real-time reporting of worker movement. Multi-location tracking at entrance and egress gates transmits alerts about workers in restricted zones, allowing organizations to quickly address noncompliance. EdgeCollector ensures that only pre-screened, pre-authorized individuals have access to designated areas, with automatic security alerts.
“EdgeCollector enabled Skanska to provide crucial security measures that APL required during construction,” said Swiftsure Group’s Bruno Riegl. “It provided flawless safeguards and supporting documentation for real-time security and potential forensics.”
RFID System Protects Restricted Site from Unauthorized Entry
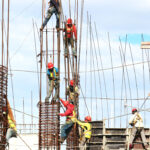
EdgeCollector documents who is where
APL is Johns Hopkins University’s scientific and engineering research and development division that spans 453 acres with more than 20 buildings at the Laurel site. Its often top secret projects for the US military, NASA and the Defense Advanced Research Projects Agency (DARPA) make detecting and tracking unauthorized personnel at the facility a top priority, including at its construction sites.
The EdgeCollector personnel tracking system used hybrid RFID/barcode-embedded identification badges, readers and event management software to track workers and others at the APL site in real-time from the main campus entry gate into any of the construction site gates. It followed the process in reverse as individuals exited the construction site to campus egress locations.
When pre-screened personnel and visitors reported to the main campus entry gate and were authorized to enter, their ID badges were scanned with a fixed location RFID reader to verify their identity. A clock started running for a predetermined period of time during which ID badges were read at the designated entry gate to the actual construction site. If a tag was not seen after that time, EdgeCollector sent a text alert to a supervisor or to security personnel to locate the person.
When leaving the site at the designated exit gate, a worker or visitor’s ID badge was automatically read to ensure that it was seen again within a certain period of time at one of the other exit gates, or back again at the main gate. If a tag was not seen, the system sent an alert to the appropriate supervisor or security personnel.
EdgeCollector Tracks Workers on the Move
EdgeCollector enables easy worker enrollment at onsite stations or via web interface, using photo IDs for enhanced identification. All ID badge read events are logged into a permanent record with associated badge number, time, location and direction of movement, such as when a worker enters or leaves an ID badge read zone. This information is housed on a secure off-site server, with web access granted to appropriate personnel.
The solution provides real-time visibility into single and cumulative event worker movement, documenting worker location by zone, viewable on a web dashboard. It sends notifications and alerts for approaching time limits within zones, and auto-generates reports by date and time, individual worker, group and subcontractor.
QuickStart Kit Makes Implementation Fast and Easy
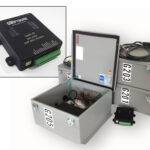
The Swift-ID SID400 reader powers the QuickStart Kit
EdgeCollector uses the QuickStart Kit, a fully functional RFID system that avoids complex on-site installation and disruption to end users’ operations. The system incorporates rfidCollect’s fully integrated, FCC approved UHF RFID reader, on-board computer with store-and-forward tag data transfer, and cellular connectivity. The kit comes with pre-installed 6-foot antenna cables and a surge protected, grounded 120 VAC power cord. A 12VDC 3A converter supplies power to the reader and computer.
The SID400 reader is a USB-connected EPCglobal UHF Gen 2 RFID reader and writer powered by Impinj’s Indy RS2000 SiP. It incorporates a 16-pin terminal block with four GPIO ports, and 5V and 12V outputs for powering ancillary devices. The reader’s system functions can be monitored through on-board LED status displays.
The SID400’s GPIO capabilities enable the reader to control a variety of devices such as cameras, locks, light bars and audible alarms. It delivers read rates of up to 500 tags per second. In addition to the device’s primary function of automatic asset/personnel identification, it provides a platform for related information distribution and alerts. It delivers read rates of up to 500 tags per second depending on tag populations, power settings and data parameters.
The QuickStart Kit includes a powerful embedded computer enabling the system to remotely process actionable data on the network edge and forward RFID and sensor-derived data to users’ backend systems. The system has a quad-core 64-bit ARM processor and supports 2.4 and 5.0 GHz IEEE 802.11B/g/n/ac 2ireless LAN, Bluetooth 5.0 and Gigabit Ethernet.
The device has a full array of communications and connectivity capabilities including POE, Wi-Fi, Bluetooth and an optional 3.75HSPA+ cellular module with antennas for use where Wi-Fi and Ethernet are not available. Two external USB ports and an SD card slot provide peripheral device and expansion functions.
About Swiftsure Group
The Swiftsure Group is a systems developer and integrator specializing in RFID- and sensor-based technologies for inventory, asset and workflow management. Since 1998 it has provided consulting services, turnkey solutions and project management for automatic data capture, resource optimization and business process improvement.
About Skanska
Skanska USA is one of the largest, most financially sound construction and development companies in the nation, serving a broad range of clients including those in transportation, power, industrial, water/wastewater, healthcare, education, sports, data centers, government, aviation and commercial. Headquartered in New York, with offices in 28 metro areas, Skanska USA has more than 9,000 employees with expertise in construction, civil infrastructure, public-private partnerships and commercial development initiatives.
###