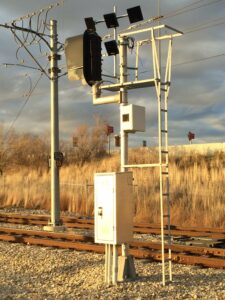
Antennas and readers capture data about UTA’s RFID-tagged light rail cars and equipment
March 3, 2015 – The Utah Transit Authority (UTA) has completed a successful predictive maintenance pilot project for its TRAX light rail system using an RFID-based automated asset management solution. It allows UTA to establish a maintenance schedule based on actual use instead of preset times that unnecessarily remove equipment from revenue service.
The system, deployed at UTA’s Jordan River Service Center in Salt Lake City, also helps UTA meet federal mandates to monitor the condition of and make timely repairs to railcars and equipment components, reducing breakdowns and ensuring efficient, safe operations.
Within two months the pilot proved that passive RFID tags attached to equipment had a 100% read rate as they traveled at 15 mph through a read zone with an array of RFID antennas and readers. Data collected at each read zone is transmitted to a dedicated UTA server hosting resource management software, where the information is recorded and linked to event notification modules for predictive maintenance.
The pilot program also showed the system boosted accuracy of asset auditing, with an error rate of less than .05% compared to 29% when conducted manually. The automated process reduced man hours, lowering labor costs and freeing staff for other tasks. In addition, the system lets UTA optimize spare parts stocking by eliminating the need to overstock for unexpected repair and maintenance, and allowing parts to be ordered as needs are anticipated.
Bruno Riegl, chief executive of the Swiftsure Group, project managed the program, which uses a system of portals, antennas, readers and RID-based asset management software. Data collected at each read zone is transmitted to a dedicated UTA server hosting the resource management software, which records and links the information to event notification modules.
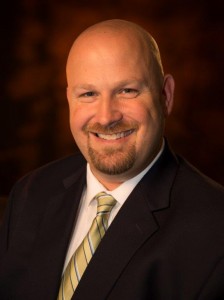
Kyle Stockley, UTA’s Transit Asset Administrator
Kyle Stockley, UTA’s Transit Asset Administrator, led the cross-functional team that oversaw system selection, design and implementation. “UTA has broken new ground in the public transit industry by linking asset management and maintenance over the life of its assets,” Stockley said. “Tracking major components installed on light rail vehicles will lead to predictive maintenance activities and more accurate useful life projections, which will lower overall cost of ownership for our agency, in turn providing better value to the community we serve.”
UTA installed RFID read zones at the entrance to its main railcar service facility so the authority could identify specific vehicles and critical components to track usage cycles for maintenance. Each zone has a set of RFID antennas installed on a signal gantry to read roof mounted equipment, and a set of between-the-rail antennas reading tags on equipment installed on the underside of vehicles. Data collected at each read zone is transmitted to a dedicated UTA server hosting resource management software, which records and links the information to event notification modules.
The solution provides UTA a platform to track the health of components by associating life miles, life hours and rebuild history throughout the useful life of equipment. By incorporating this previously unavailable data into its asset management model, UTA can perform predictive maintenance and asset lifecycle analytics.
UTA, which runs more than 225 rail cars and engines and 1,000 surface vehicles, was recognized as the outstanding large city transit system in 2014 by the American Public Transportation Association System.
Since 1998 the Swiftsure Group has provided an independent perspective on planning and implementation of operations process improvement. Its consultants are RFID and system integration experts who combine best practices in inventory, asset and resource management to improve asset lifecycle and inventory management for clients worldwide.